This audio is auto-generated. Please tell us what you have feedback,
Closen Pickle Brand detects its roots over 150 years ago Claus F for an Illinois farmer. There was a truck load of a cucumber named Closen that he could not sell. Instead of throwing them, they turned them into pickle.
Today, making pickle is a big business. Brand owner craft hyge process About 60 million Cucumber annual to make broadly 42 million The top-bound Kleseen’s jars Refrigerated Pickle brand. But making crisp spears is not always easy.
Cucumbers that turn into closen pickles go from vine to brine in 10 days or less, which gives a small room to the craft henz for error. It is paramount that Craft Hanz knows what Cucumber Klesen is coming to the plant Illinois It seems that it can prepare – different circumferences, lengths and bending plans can wreak havoc and require changes in the production line where the spear is processed.
In recent years, Craft Hanz has included artificial intelligence in several aspects of its supply chain, so that to increase capacity and reduce costs. Cucumbers and its Closen Pickle Brands have been one of the largest beneficiaries of the once-report technology.
North America Logistics and Planning in Craft Hanz sat down with food dives to discuss the impact of artificial intelligence on the company’s supply chain and Closene, One of its top-bound consumer brands In its category,
This interview has been edited for brevity and clarity.
Food Dive: How did Craft Hange reach the point where he can apply to AI in its supply chain?
Bill Durbin: When we talk about the overall company change, … the supply chain has played a very important role within it, ensuring that we are continuing to develop efficiency, until then in marketing And are able to reinstall back to our businesses, be able to increase revenue and improve our performance.
For the supply chain change, I think it was about actually about being fantastic on the basics and improving our processes and identifying the best practices, then rolling from the other side Our 60 manufacturing facilities, Warehouse and distribution centerAnd so a very manual effort to deliver us there, but we identified a lot of benefits by identifying the best ways to do something and then continued to increase that time and increase that time.
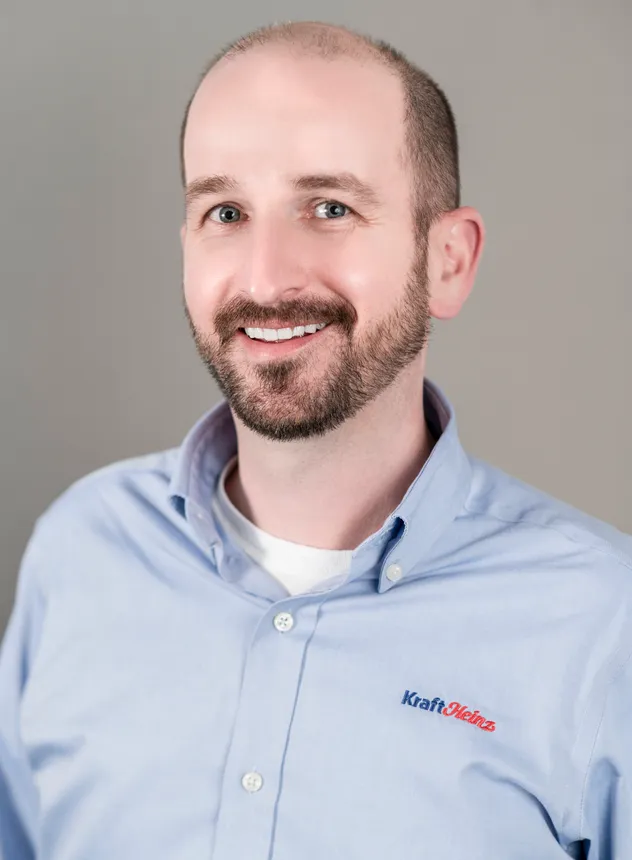
Bill Durbin, Head of North America Logistics and Plan in Craft Hanz,
Permission given by Craft Hanz
But over the last few years, we actually stopped this digital journey, where we are able to accelerate that change. Taking advantage of better equipment and improving the visibility of exceptions within the network, and then taking advantage of things like machine learning, we are able to get people out of those manual transactions so that they then then they then adapt to the supply chain Can help run. , Vs to be in the day -day transaction.
When did Craft Hanz start using AI for cucumber for the first time and how did the idea come?
Durbin: We started it about a year ago. Our cucumber supply chain is very low. This is 10 days from the ground when it comes in a jar. During some time of the year, we make a source of cucumber from the fields close to the manufacturing facility, and during winter, we are sources from warm areas that lead to long transit time. In many of our processes, we can buffer with inventory if goods are received and they are not at all specifications.
There are ways to reduce it, but with such a small supply chain, it is super important that we recognize the issues as soon as possible and then make sure that we get the shape correct so that we can achieve the best skills. Because we run those things down. Line. This allows us to get the best quality cucumber and the best quality pickle at the end.
With pickle, the perimeter matters, size matters, length matters, cucumber turns, depending on all the things they are, depending on this, we will work differently within the site, Also quality. If the quality does not meet our specifications, we cannot run it.
We started bringing cucumber batches, taking pictures of those batches and the quality team was getting the response to which they were For specificationTo validate, shape them. We were training the machine to do the same task.
Similar to that pre -example, over time, we trained and then a variety of defects, different types of sizes, what those things meant. And then [AI] Learned from himThe beginning of identifying these variations, And the operator will validate those things. So now it is capable of identifying those things.
Being able to do this, we can achieve that level of certainty on that product, we can immediately address it, so we know that it is to be sent inside the factory, or if it is an issue, then We can achieve that real -reactions to be able to address suppliers.